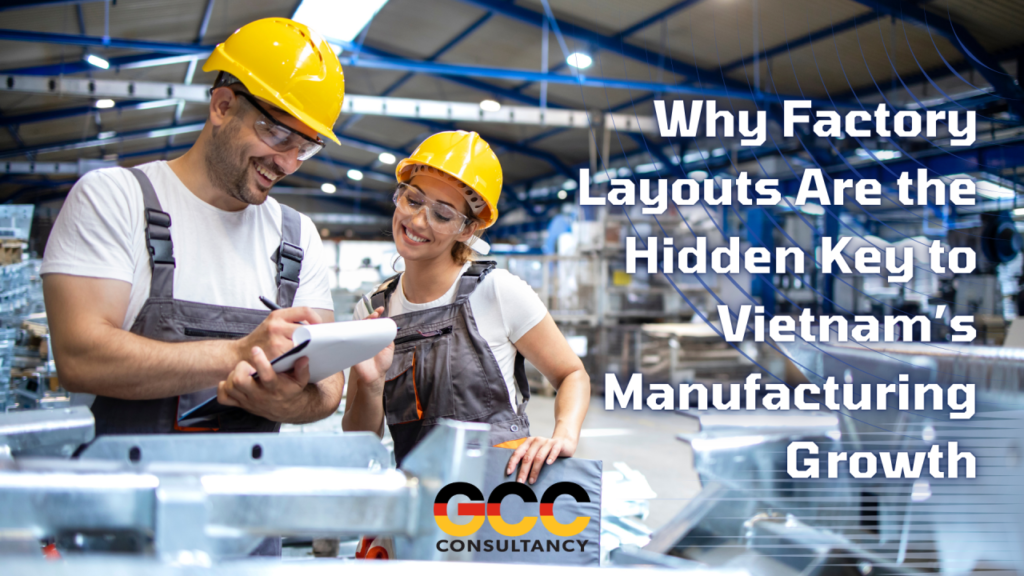
Vietnam’s manufacturing sector is booming, with global giants shifting production to the country. But behind the scenes, many factories are held back by an invisible bottleneck: outdated factory layouts.
The Hidden Cost of Poor Layouts
A factory’s physical design impacts everything:
- 🚚 Material Flow: Congested pathways delay production.
- ⏳ Downtime: Poor machine placement wastes hours daily.
- 💸 Energy Waste: Inefficient workflows spike electricity bills.
For Vietnam to compete globally, factories need layouts optimized for speed, flexibility, and Industry 4.0 integration.
3 Challenges Unique to Vietnam
- Rapid Scaling: Many factories grow haphazardly, leading to chaotic workflows.
- Legacy Infrastructure: Older facilities struggle to adopt automation and IoT.
- Skill Gaps: Teams lack training to manage tech-driven layouts.
How GCC Transforms Layouts for Growth
✅ Data-Driven Design: Use 3D simulations to test layouts before implementation.
✅ IoT Integration: Embed sensors to track bottlenecks in real time.
✅ Lean + Industry 4.0: Merge lean principles with smart tech (AGVs, AI-powered MES).
Case Study: A Ho Chi Minh City Electronics Factory
After GCC redesigned their layout:
- 📈 Output Increased
- 🔌 Energy Costs Fell
- 🚚 Material Handling Time Dropped
Vietnam’s Opportunity
With FDI surging, factories that optimize layouts today will dominate tomorrow. GCC’s local expertise ensures solutions fit Vietnam’s unique needs:
- 🇻🇳 Vietnamese-speaking consultants.
- 🛠️ Cost-effective upgrades for SMEs.
- 🔗 Seamless integration with ALPHACAM, CAD/CAM, and ERP systems.
Ready to Unlock Growth?
📞 Book a FREE Quotation: Let GCC’s experts identify your hidden inefficiencies.
This is so informative!